Harnessing Construction Data to Deliver Pre-Construction Efficiencies with RLB - Digital Builder
Harnessing Construction Data to Deliver Pre-Construction Efficiencies with RLB - Digital Builder
Rider Levett Bucknall (RLB) is an independent global construction and property consultancy providing management and advice throughout the built environment. Committed to creating value for their clients and achieving commercial success alongside project and programme success, the team provides independent expert advice to their global client base. Through their extensive expertise in cost management and quantity surveying, project and programme management, asset advisory and specialist consultancy, RLB have over 4,000 people working across 40 countries worldwide.
With a sharp focus on flawless execution today for a better tomorrow, RLB are committed to combining fresh perspectives with sector expertise. To achieve better outcomes for clients and for the construction industry globally, RLB have been exploring the value that can be realised and incorporated into projects through a more joined-up pre-construction process and through integrating digital workflows into working practices.
Gaining Better Outcomes through Shared Data
RLB identified that it needed to enhance their information sharing practices on projects they had been asked to support in the pre-construction phase. For their cost management activities, the team recognised that to address this specific problem but to also achieve long term success, a digital roadmap would be necessary to support the team connect into a central source of truth better. Many of RLB’s projects involve multidisciplinary teams and a number of stakeholders, so ensuring the most up-to-date and accurate information related to the project was a key driver when it came to introducing digital workflows.
“We needed a change in mindset and our processes to reimagine the design and pre-construction phase across the industry to improve collaboration and share data. One central source of truth which we could extract real-time data for design coordination and review, quantity-take-off, and mark-ups is essential,” says Allan Trotter, Digital Lead for Cost Management at RLB. “Not having accurate information causes a barrier when it comes to digitalisation across our group as some colleagues would revert to 2D ways of working because they didn’t have access to all of the information they needed to work in 3D,” reflects Allan.
Removing Inefficiencies and Duplication through Investment in Digital Workflows
This led to working in a way that involves time-consuming and manual processes which were not joined up or standardised. These workflows would sometimes lead to the ineffective duplication of work as tasks were repeated that had already been completed earlier in the construction process. RLB decided to take action and to look at what technology investments they could make to standardise ways of working to lead to better outcomes for their clients and the industry as a whole.
Autodesk Construction Cloud’s Assemble solution connects BIM data to support estimating, change management, scheduling, tracking and design review processes.
Leveraging BIM data from design to construction with Assemble would help the teams at RLB to work in a more connected environment that supported cross-team and industry collaboration. The UK team decided to invest in piloting the technology on behalf of the global organisation to determine the benefits it could bring. “Assemble is a solution that sits in between lots of different processes and systems, it was easy and intuitive to use so we didn’t need to undergo lengthy training courses,” says Allan.
Piloting for Proof
RLB tested their new Assemble workflow on a large power plant project in the UK where they were asked to carry out a cost verification exercise and quantity checks on the tender issue information for the construction design stage of the project. The team used other Autodesk solutions as part of this project including Revit and Navisworks which could then be linked with Autodesk Construction Cloud’s Assemble. “We used solutions from Autodesk’s AEC collection to check the information model and condition the model for quants takeoff and further costing,” says Allan. This took place in addition to the team’s usual quality take off process which integrates Autodesk’s solutions into RLB’s own in-house cost estimating software, ROSS 5D. “Once the information model is checked and conditioned, we import the information into our ROSS 5D cost estimating software using the extended properties. This means we can utilise and standardise the model mapping process for our team,” comments Allan.
Improving the model checking and conditioning process means RLB is able to identify errors and gaps quicker and ensure the information is suitable for quantity takeoff. This means their team could quickly create an accurate and detailed cost estimate in the required output format to improve the comparison and verification process. The feedback that the project team members shared demonstrated the benefits of using a more digital way of working for this quantity take off process at the pre-construction phase. “Everyone in the team could collaborate and work more effectively using Autodesk Assemble and we found the user experience was excellent. Our business has now adopted hybrid working arrangements, and Autodesk Assemble allows everyone to work together remotely in a way that appeals to everyone,” reflects Allan.
Adding Models in Pre-construction Requires a Change in Mindsets
Creating a single source of truth through Assemble on this project meant that the repetition of tasks was reduced and collaboration within the team improved too. Allan says: “Having information centralised in the same suite of products helped facilitate faster design and quantity checks. Before this, information could be fragmented and held in silos. Of course, there is still an element of this when working with multiple stakeholders but now we can see the technology allows us to collaborate better so our focus now must be changes to mindsets in the industry.”
RLB’s team have found the visualisation functions the most beneficial and the further reporting features will also help their teams gain more insight from project activities. “The Power BI add-in and report templates will help us dive into further analysis aiding collaboration,” says Allan. Whilst the solution has been relatively straight-forward to implement, Allan and the team know the value that a structured change management process can provide and have set up learning programmes around this as well as identified technology champions to support other users to get accustomed to using the technology.
“Our plan is to use more and more of the features available, but we are focusing on getting the basics right and ensuring everyone feels confident using Assemble currently,” says Allan. RLB hopes to extend using the technology through the design development stages of future projects so that the benefits they achieved on the UK power plant project during the tender analysis process can be extended further into the construction process creating a more streamlined and productive way of working.
“Everyone in the team could collaborate and work more effectively using Autodesk Assemble and we found the user experience was excellent. Our business has now adopted hybrid working arrangements, and Autodesk Assemble allows everyone to work together remotely in a way that appeals to everyone,” – Allan Trotter, Digital Lead for Cost Management at RLB
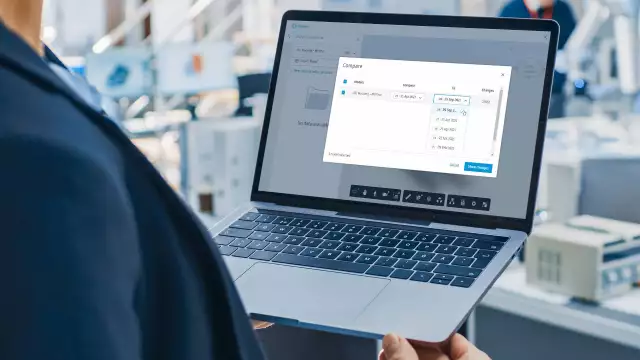